Copper alloy is an alloy made of pure copper with one or several other elements as the base. It is mainly used to make electrical equipment such as generators, bus bars, cables, switchgear, transformers, etc, and heat-conducting equipment such as heat exchangers, pipes, and flat plate collectors for solar heating devices.

Physical properties of copper alloy
Excellent physical and chemical properties
- Excellent electrical and thermal conductivity.
- High resistance to corrosion of the atmosphere and water, and copper is an anti-magnetic substance.
- Good processing properties: very good plasticity, easy cold, and hot forming
With some special mechanical properties
For example, excellent friction reduction and wear resistance, high elastic limit, and fatigue limit, such as beryllium bronze.
Pure copper is a rose-red metal, the surface is purple after the formation of copper oxide film, so industrial pure copper is often called purple copper or electrolytic copper. Density is 8-9g/cm2, melting point 1083°C.
Pure copper conductivity is very good
- Used in large quantities in the manufacture of wires, cables, brushes, etc.
- Good thermal conductivity is commonly used in the manufacture of magnetic instruments, instruments to prevent magnetic interference, such as compasses, aviation instruments, etc.
- Excellent plasticity, easy to hot pressing, and cold pressure processing, can be made into tubes, rods, wires, strips, strips, plates, foils, and other copper materials.
- There are two kinds of pure copper products: smelted products and processed products.
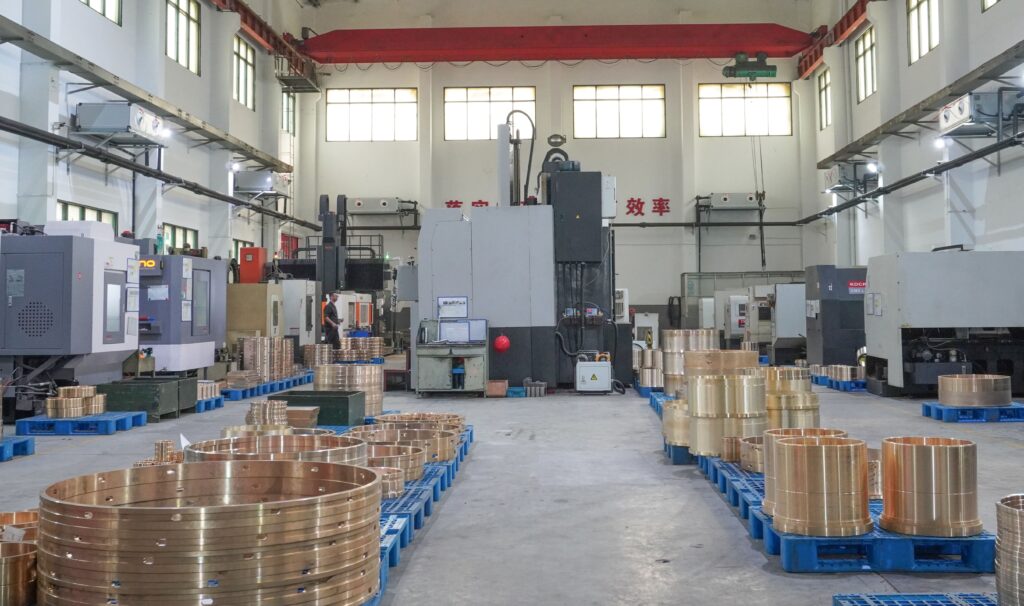
Classification of copper and copper alloys
Casting ordinary bronze
With excellent casting properties and high mechanical properties, machinability can be welded, good corrosion resistance, with a tendency to stress corrosion cracking.
Casting aluminum bronze
High mechanical properties, casting properties, corrosion resistance, stress corrosion cracking tendency, can be welded. High denseness, good corrosion resistance, as wear-resistant parts working temperature is not greater than 400 degrees, can be welded, but not easy to braze.
Casting lead bronze type.
Have a high lubricating performance, in the lack of lubricating medium and water as the medium has particularly good self-lubricating properties, suitable for bimetallic casting materials, corrosion resistance, easy cutting, casting poor.
Structural materials have a good oxidation performance when the temperature of the feed water is 90 degrees and conductivity of about 10-14MS / m.
Casting manganese bronze class
Having high mechanical properties and corrosion resistance, casting performance is good organization stability when heated. Application in air, fresh water, seawater steam, and a variety of liquid fuel parts and valve bodies, valve stems, pump joints, as well as the need to cast pasteurized and tinned parts.
Casting silicon bronze type.
Has high mechanical properties and good corrosion resistance, good casting performance, high fluidity, dense casting organization, and good gas tightness.
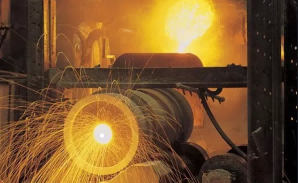
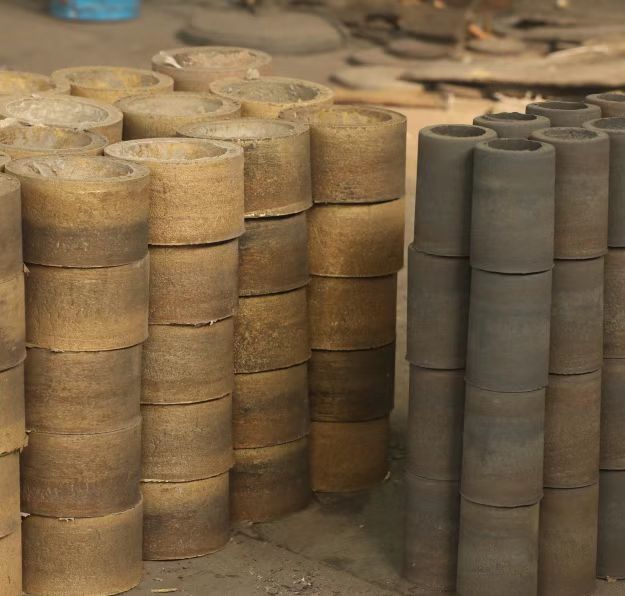
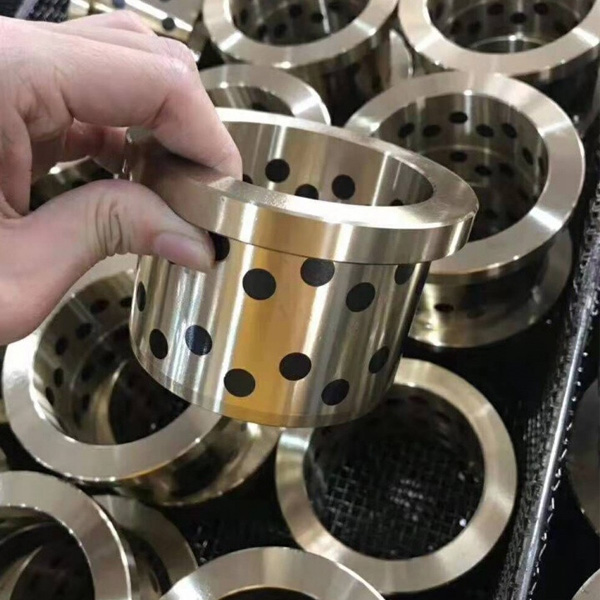
What are the ways of strengthening copper alloy materials?
Fine grain strengthening
The effect of fine grain strengthening can be expressed by the Hall-Petch relationship, the grain size decreases, and the strength of the alloy increases.
This is because the dislocations are blocked by the grain boundaries during the deformation of the polycrystal, and the dislocations accumulate on the surface of the grain boundaries so that the slip band that stays at the grain boundaries generates stress concentration at the top of the dislocation accumulation group; the dislocation accumulation group can interact with the applied stress, and when the stress is large enough to activate the dislocation source inside the adjacent grains, the slip band can be transmitted from one grain to the next.
As the grain boundaries and adjacent grains are oriented differently, this hinders the movement of dislocations from one grain to another. The finer the grain, the larger the volume of grain boundaries per unit volume, and the greater the resistance to dislocations, the higher the strength of the material.
Since the crystal conductivity is independent of crystallographic orientation, grain refinement only increases the grain boundaries, and thus has little effect on the electrical conductivity of copper. In addition, grain refinement can improve the plasticity of the material while increasing its strength.
This is due to the grain refinement, the material deformation at the grain boundaries of the stress concentration caused by dislocation plugging can be effectively relieved, delaying the emergence of cracks, before the material fracture can achieve a larger amount of deformation.
In order to obtain fine-grain organization, several methods can be used.
- Changing the solidification conditions during the crystallization process, such as the rapid solidification method.
- Deformation with recrystallization to refined grains.
- strong plastic deformation methods, using desolvation reactions, spindle decomposition, powder sintering, internal oxidation, etc. to produce a diffuse second phase within the alloy to limit the grain growth of the matrix tissue.
- Grain refinement by multiple iterations of isomeric transformation.
- Refining grains by adding some trace alloying elements. Rare earth has a significant refining effect on copper alloys grains and can significantly refine copper alloys grains.
Copper alloy manufacturers teach you how to identify pure copper
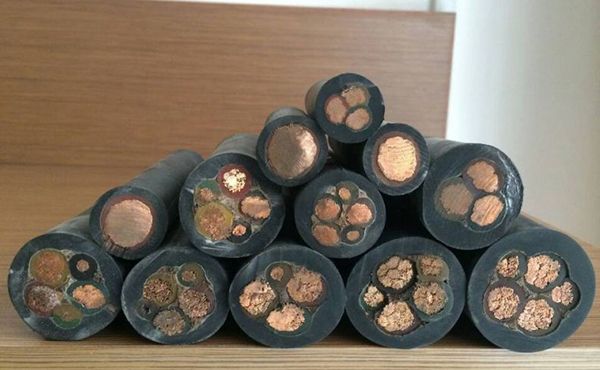
The methods of identifying pure copper are checking hardness, looking at stubble, bending method, and throwing method.
Check the hardness
The higher the color of copper jewelry, the softer the texture, the whiter and brighter the surface. Take about 60 grams of copper bracelet for example, such as a hand pull on the open, no elasticity, its color in about 95%; such as a little elasticity, color is about 80%-90%; such as elasticity is larger, color is below 70%.
Look at the stubble
Cut or fold the copper jewelry to see the color of the stubble. If the jewelry is soft, stubble thick and soft, and slightly red, the color is about 95%.
- If bending hard by hand, stubble white and gray, or slightly red, the color is about 90%.
- If hard, the stubble is light red, yellowish-white, or grayish, with a color of about 80%.
- if bending hard, the stubble is slightly red, slightly yellow, earthy yellow, and other colors, the color is about 70%.
- If the stubble is red with black, or yellow with black, the color is less than 60%.
Bending method
- Pinch bending with your fingers, high color soft and pliable, easy to bend, and not easy to break.
- The quality of the next bending harder, or barely bend, and some even can not be bent with the finger.
- Copper wrapped by bending or hammering a few times will crack; fake can not withstand bending, easy to fracture.
Throwing method
High-color copper jewelry, thrown on the table board jump not high, there is a “poof” sound; fake or low-color is light, thrown on the table board bounced very high, the sound is relatively crisp.
Copper alloy manufacturers to introduce the difference between pure copper and purple copper

Pure copper is a purplish red metal, commonly known as “purple copper”, “red copper” or “red copper”, rich in ductility. Pure copper, the size of a drop of water, can be drawn into thin wire up to two kilometers long or calendered into an almost transparent foil larger than a bed.
The valuable property of pure copper is that it conducts electricity very well, second only to silver among all metals. However, copper is much cheaper than silver and is, therefore, the “mainstay” of the electrical industry. Pure copper is much more versatile than pure iron, and every year 50% of copper is purified by electrolysis to pure copper for the electrical industry.
Copper alloys manufacturers describe pure copper, as containing more than 99.95 percent copper. Very small amounts of impurities, especially phosphorus, arsenic, aluminum, etc., reduce the electrical conductivity of copper.
Copper containing oxygen (copper refining easily mixed with a small amount of oxygen) has a significant impact on the electrical conductivity, copper used in the electrical industry must generally be oxygen-free copper.
In addition, lead, antimony, bismuth, and other impurities will make the crystallization of copper can not be combined together, resulting in thermal embrittlement, which will also affect the processing of pure copper.
This very pure copper is generally refined by electrolysis: impure copper (i.e., crude copper) is used as the anode, pure copper as the cathode, and copper sulfate solution as the electrolyte. When the current passes, the impure copper on the anode gradually melts, and the pure copper gradually precipitates on the cathode. The copper thus refined can be 99.99% pure.
How to identify the types of copper alloys
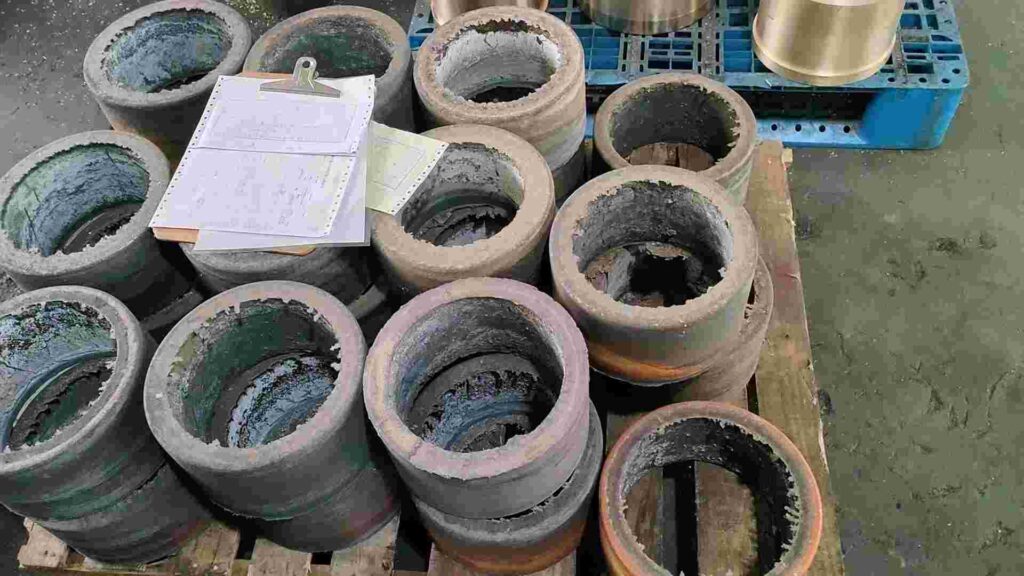
White copper, brass, red copper (also known as “purple copper”), and bronze (greenish gray or grayish-yellow) are distinguished by their color. Among them, white copper and brass are very easy to distinguish; red copper is pure copper (impurities <1%), and bronze (other alloy components of about 5%) is slightly difficult to distinguish.
When not oxidized, red copper color brighter than bronze, bronze is slightly green or yellow dark; after oxidation, red copper becomes black, bronze is lime green (harmful oxidation of more water) or chocolate color.
Classification and welding characteristics of copper and copper alloys.
(1) Pure copper: Pure copper is often referred to as purple copper. It has good electrical conductivity, thermal conductivity, and corrosion resistance. Pure copper is represented by the letter + T (copper), such as Tl, T2, T3, etc. The content of oxygen is very low, not more than 0.O1% of pure copper is called oxygen-free copper, with TU (copper-free) said, such as TU1, TU2, etc.
(2) brass: zinc is the main alloying element of a copper alloy called brass. Brass with + H; (yellow) said such as H80, H70, H68, etc.
(3) bronze: the previous alloy of copper and tin called bronze, now in addition to brass copper alloy called bronze. Commonly used are tin bronze, aluminum bronze, and Min bronze. Bronze is indicated by “Q” (green).
Copper and copper alloys welding characteristics are:
① difficult to fuse and easy deformation; ② easy to produce thermal cracking; ③ easy to produce porosity
Copper and copper alloy welding mainly uses gas welding, inert gas shielded welding, submerged arc welding, brazing, and other methods.
Copper and copper alloys have good thermal conductivity, so they should generally be preheated before welding and use large linear energy welding. Tungsten hydrogen arc welding adopts DC positive connection. In gas welding, copper uses a neutral flame or weak carbonization flame, and brass is a weak oxidation flame to prevent the evaporation of zinc.
Analysis of the metallographic organization of copper alloys
Generally, the material is required to analyze the metallographic, to achieve the purpose of understanding the material organization, metallography can know the material microstructure morphology, and can initially determine the relevant properties of the material, but different materials have different metallographic organization, phase, r phase, B phase, etc.
Sometimes from the metallographic diagram can be seen that the side grains are significantly larger than the middle part of the grain, so it can be known that the side cooling is stronger than the middle part, and its nucleation trend potential energy is greater than the middle part, the number of nuclei, the number of grains is relatively small, while the casting billet cooling is quite uneven.
The dendritic growth direction of the cast billet has obvious directionality, i.e., gradient direction growth.
The cast billet dendrites are well-developed and benefit from the process processing of hot extrusion and are prone to cracking and even central holes using cold drawing.
Phase organization is mainly two phases a phase and B phase, darkening for the ordered solid solution B phase, the phase at room temperature for the hard and brittle phase, high temperature for the soft and tough phase easy to process, dendrites coarse also need to pay attention to the aggregation of high melting point substances, easy to lead to copper alloy drawing cracking, rolling skinning, cracking problems.
What is the distinction between copper alloys and copper?
A simple method is to “rub the color”, using a piece of fine sandpaper on the identification object polished, such as revealing the rose-red is copper, except for the color are different types of copper alloys. In order to determine the correct color of copper alloys, you can first find an enameled wire or wire sand to see, if they are copper and not copper alloys.
Copper is composed of copper elements alone, even if there are other metals present, it is a very small amount of impurities in the state of existence. Copper alloy is different, it is composed of copper and other metals alloy, such as copper-zinc alloy for brass, copper-tin alloy for bronze, copper with beryllium for beryllium bronze, copper-aluminum-iron alloy for aluminum-iron bronze, etc.
Copper is softer, the elongation is larger, copper alloy is harder, and the elongation is slightly smaller. Applications are generally for conductive parts, such as sinks, wires and cables, enameled wires, etc.
Copper alloys are used in a wide range of applications, from screws and nuts to waveguides, springs and reeds, early pull chains, lamps, and lanterns, and so on. Copper is relatively soft and suitable for making copper wire and fiber optic cable.
The hardness, temperature resistance, and friction of copper alloys are not quite the same as copper. Copper alloy is through the smelting of copper, so the application is more extensive, steam locomotives: tractors, combine harvesters, crop sprayers, bulldozers, graders, and other construction machinery.
automotive industry for power steering pumps, steering thrust shims, disc brakes, shock absorbers, door hinges, wipers, chair adjusters, air valves and solenoid valves, etc.
Office business machinery: copiers, fax machines, printers, mail processors, etc.
Hydraulic components and valves: gear pumps, piston pumps, vane pumps, ball valves, butterfly valves, cylinders, oil cylinders, and other hydraulic components, etc.; household appliances: refrigerators, air conditioners, vacuum cleaners, sewing machines, washing machines, microwave ovens, and fitness equipment, etc.
Other logistics machinery, packaging machinery, textile machinery, port machinery, mining machinery, forest machinery, etc.
Cutting properties of copper alloys
The general cutting properties of copper alloys are poor. Adding elements such as lead, sulfur, and tellurium can improve the cutting properties of copper alloys.
According to the good and bad cutting properties, copper alloys can be classified as
Free-cutting alloys with machinability above 70%, including free-cutting copper containing lead, sulfur, or tellurium, free-cutting brass, various lead brass, and bronze, and zinc white copper containing lead at about 2%.
Cutting properties of 30% to 60% of the medium cutting alloys, including 60% to 85% of copper brass and lead-containing about 1% of bronze and zinc white copper, etc.
Hard-to-cut alloys with machinability below 20%, including low-zinc brass, zinc white copper, tin bronze, copper-nickel alloy, beryllium bronze, etc., are generally compared with a machinability of 100% for easy-to-cut brass.
The stress relaxation resistance of beryllium bronze, white copper, and zinc white copper is Z good, followed by tin bronze and tin brass, followed by silicon bronze, and the stress relaxation resistance of ordinary brass is poor.
On the point of stress relaxation capacity, the use temperature of copper alloy is about 200 ℃. Brass with low-stress relaxation resistance can only be used to make parts slightly above room temperature, beryllium bronze, and ternary copper-nickel alloys with tin, silicon, aluminum, or zinc.
Even at the high temperatures commonly used in current devices, their resistance to stress relaxation is still quite high. Some brasses, bronzes, and white brasses are widely used in the manufacture of automotive radiators, heat exchangers, and components for various industrial devices that require rapid heat transfer through, or along, the metal. Brass, some bronze, and white brass are used in the manufacture of condensers, pipes, and valves that require corrosion resistance in systems that convey gas and liquids.
For example, copper brazing material is used for brazing metals, superplastic copper alloys are made into various devices by superplastic forming, and functional copper alloys are used to make coins, ornaments, musical instruments, etc.
In addition, a variety of copper alloys are also indispensable materials for the mechanical industry, to process into springs, fasteners, pads, and other mechanical parts.
Nickel silver, brass alloys, copper zinc alloys, beryllium copper, silicon copper, aluminum bronze, and high copper alloys are all in the section of metal alloys, cast copper alloy in chemical proportions to get superior electrical and thermal conductivity.
Bronze alloys, naval brass, copper-based alloy, phosphor bronze, high-performance alloys combined with high purity copper, and other copper alloys can be made into resistance to corrosion bronze bushings with excellent corrosion resistance because of the needs of the industry.
Copper alloys also need to consider the ultimate tensile strength, saltwater corrosion, copper electrical wiring material is also one of the good and bad electrical properties, electrical and thermal in energy conversion can refer to the heat exchangers products.
After heat treatment, the tin brasses have a high degree of improvement in fatigue resistance, thermal conductivities, and hardness values. The cold working and cold-formed alloy have excellent resistance. The radiator cores copper finned tube needs to have a certain level of corrosion resistance, this is not a saltwater pipe, the high requirements need stainless steel tube.
Other alloys made of base metal, special alloys, nickel, etc., or copper alloys will determine whether the metal has good ductility because of the high or low content of other components such as zinc in them. Nonsparking tools such as industrial press require copper alloys to have excellent conductivity, and the addition of other materials will have different industrial applications. We will talk about these materials in the next article: nickel silver, copper-zinc alloys, silicon bronze, aluminum bronzes, naval brass, bell metal, and their relationship with pure copper. Cast copper alloys have been talked about in the article “Bronze Bushing Casting”, will also be a separate talk about the metal alloys, high copper alloys tensile strength and zinc content.